Restoration of the
Temple of Diana
Sonnenber Garden
Written By Casey Bolles & Zach Daddis
January 1, 2025
An up close look at BAC’s step-by-step process in this ground up restoration.
Project Description
Resurrecting the Temple of Diana at the Sonnenberg Gardens
Originally, the Sonnenberg Gardens was the summer home of Mary Lee Clark and Fredrick Ferris Thompson, one of the founders and first vice president of what is now Citibank. After Mary passed in 1923, her nephew inherited and subsequently sold the estate to the federal government. For a period, the Mansion was used to house doctors working for the adjacent VA hospital. Eventually, the property was turned over to a local nonprofit, and finally, in 2005, the NYS parks department purchased the property. Today, the park is run by a nonprofit, though it operates as a state park.
The Temple of Diana was built around 1905, originally made from cast concrete—a hulking, scalloped dome sitting atop 6 fluted composite style columns with extensive embellishment, forming the lavish home for “Diana Robing,” a signed Bazzani statue, which is a copy of “Diane de Gabii.” The original Diane de Gabii, commonly attributed to Athenian sculptor Praxiteles, was excavated in 1792 by Gavin Hamilton and sold to Napoleon Bonaparte, who housed it at the Louvre, where it remains to this day.
In 1999, the Temple of Diana was disassembled due to safety concerns. In 2024, the Sonnenberg Gardens contacted Buffalo Architectural Casting to restore the temple to its original grandeur. An employee at Sonnenberg, who had been to our studio in Buffalo for a workshop years ago, reached out about the Temple of Diana, and connected us with the executive Director, David Hutchings.
After explaining the process for rebuilding the historic tempietto, we scheduled some time before the snow fell to make molds of any of the original ornament that was still in tact, and gather dimensions from anything we could in the field.
Currently, we’ve cast plaster models from the molds we took on site and are resculpting in any of the missing ornamentation, some of which we have only historic photographs for reference. When the sculpture is complete, we will make molds to cast from, develop a color and texture match to the original stone, and fabricate the structural skeleton to which our pieces will be attached.
The final step will be to assemble everything on site, after which we’ll have some remarkable before and after photos to include in a future article.
Check out the video to see some scenic footage from our onsite mold work.
Technique Highlight
Making Rigid Molds from Original Ornamentation
When original highly sculptural architectural ornament is being replicated, the best case scenario is that there’s some original pieces to make molds from. The most difficult scenario is when there is no original ornamentation, and pieces must be sculpted from scratch, only utilizing historic photos and site dimensions as reference.
Somewhere in between is sort of a hybrid scenario– the basic shape of the original pieces are intact, and some of the ornament is there, but some sculpting still needs to be performed in order to fill in the detail. The Temple of Diana falls into that middle category. So while sculpture work is still necessary, extensive on-site mold making was necessary too.
Broadly speaking, we make molds in two ways: with a gypsum mold, or a rubber and mother mold. Gypsum molds are generally quicker, lighter weight, and more cost-effective, but because they’re rigid, they can’t capture deep details with heavy undercuts (places where a detail is so dimensional that a rigid mold would get locked into place and be impossible to demold).
If you made a rigid mold of, say, a statue’s hand, then the only way to demold it would be to cut the rigid mold around each finger.A rubber mold, on the other hand, can flex around deep details and undercuts. So a mold of the same hand may require, for instance, a slit around one side, but one might be able to essentially pull the rubber off like a glove. This is a bit of an oversimplification, and there is larger variety of mold materials we may use for a given piece.
Forton-MG is a polymer-modified gypsum made with alpha gypsum, polymer, resin, and hardener. This means that no water is needed in the mix, and the cast molds are lightweight and very strong. Conventional plaster/GRG (fiber-reinforced gypsum), in comparison, is very heavy and brittle. Using a these additives means that the molds will be easier to transport, store, and work with in-studio. For the capture of details on site for the Temple of Diana, we used a type of rigid gypsum-based mold called Forton-MG, as, while there is a lot of detail, not much of it contains undercuts.
Because much of the fine detail has been lost to time and erosion, these rigid molds very accurately capture the broad shapes of the original pieces, over which we will ultimately hand-sculpt finer details.
While at the Sonnenberg Gardens, we took molds of the extrados of the dome (the outside of it), the column shafts, and the lintel, the top of which forms the springing of the dome proper (i.e. the point from which the dome rises).
Because mold making is more consistent in a more controlled environment, any pieces small enough to transport were taken back to our studio in Buffalo to be molded there. This included column capitals, bases, and the finial.
The damaged pieces brought to our studio can be sculpted directly onto, and so the final casting molds will be made from these sculpturally-repaired models. The site molds, since they’re taken from damaged ornament, will not have the final pieces for the replacement temple cast from them. First, we’ll cast plaster models to repair, and then we’ll make rubber molds to cast GFRC into in order to produce the pieces which will be used to assemble the temple’s structure.
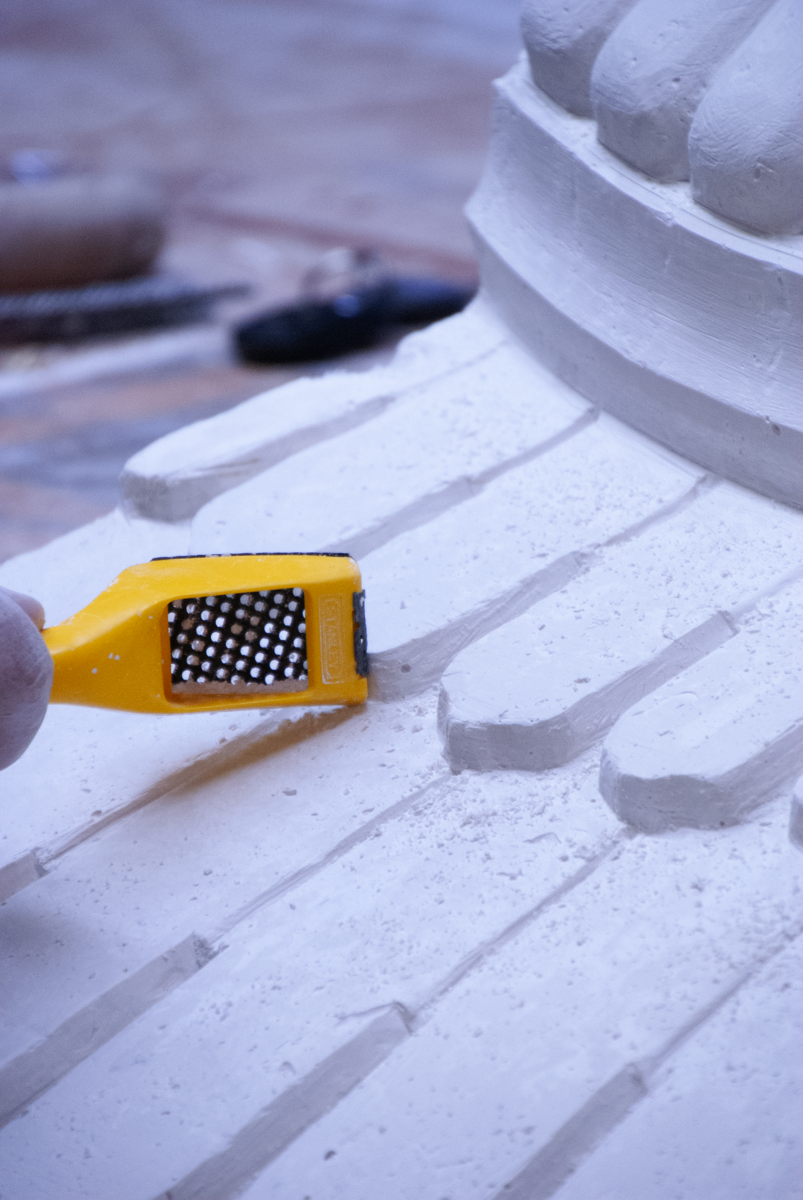
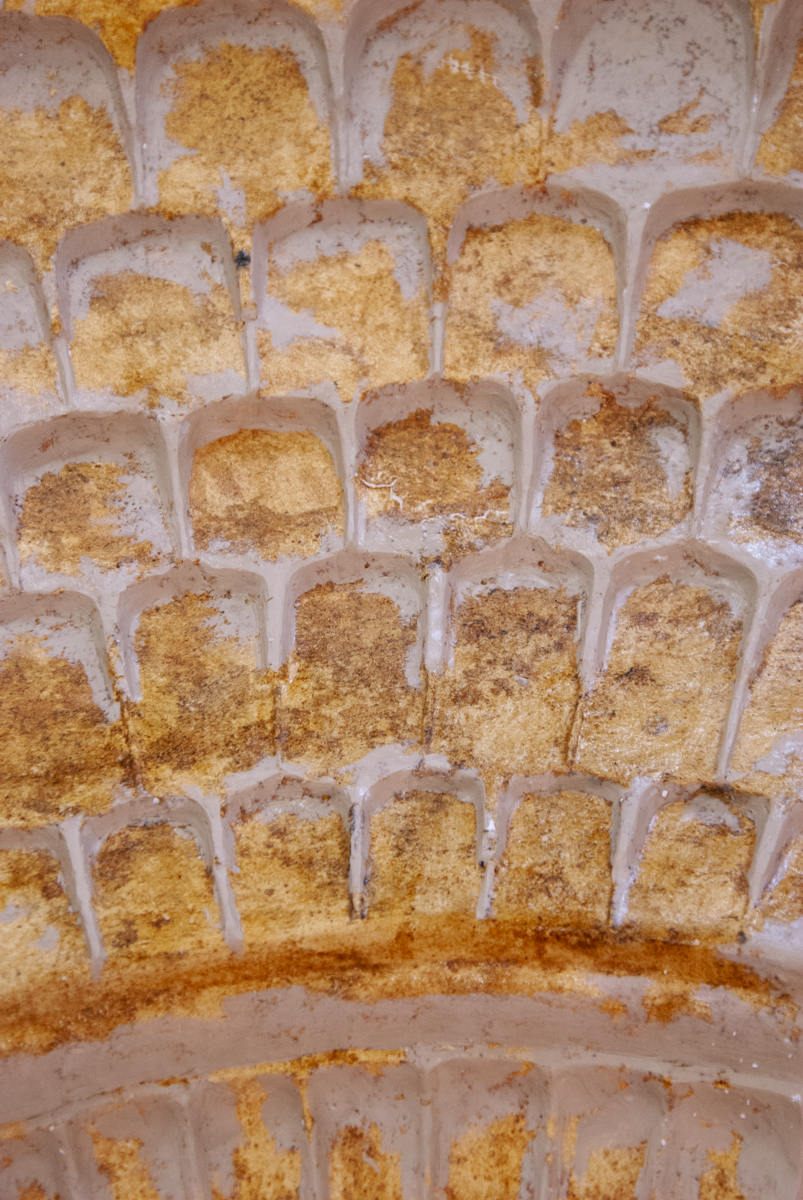



